NiteOwl
Pack Dog
- Joined
- Dec 31, 2012
- Messages
- 98
- Reaction score
- 0
- Location
- Office Adventurer
- Bike
- Honda XRV 750 Africa Twin
At 125 kkm, my Africa Twin has probably reached its economic half-life thirteen years after I bought it. It was one of the last XRV750Y models sold at a 12.5% discount when Honda decided to terminate one of its iconic models in deference to the GS onslaught.
It's never let me down and has enabled me to experience Southern Africa in a way I could never have imagined. The engine still runs with that inimitable V-twin purr, but the creeping at traffic lights, stiff gear-change and oil consumption eventually prompted me to "take a look". Those who have down this road before will immediately recognise the symptoms of motorcyclis restoritis, a debilitating affliction which can only be cured by
🖌 ⏲ and 
I'm not into bling, and prefer to avoid modifications to my vehicles as they often compromise something else. So the end purpose is simply to get the bike back into a reliable and usable condition for the next hundred thousand km, rather than into a concours or (horror) sellable state.
Of course I also did the logical thing and attended the New Africa Twin Road Show and tried the modern reincarnation of my, um, classic version beforehand. It was seductive. I liked the ride, the engine, the ABS... but not the sticker-shock of nearly three times the original price. At moments like these, rational thinking :3some: takes over: my old bike is still fine, It's set up the way I like it, I don't need so much power, all this electronic stuff can’t be fixed in the bush, I'm not riding that much anymore. Etc. etc.
So here is an invitation to join me on my journey of discovery in an attempt to reverse 13 years of accumulated wear and tear.
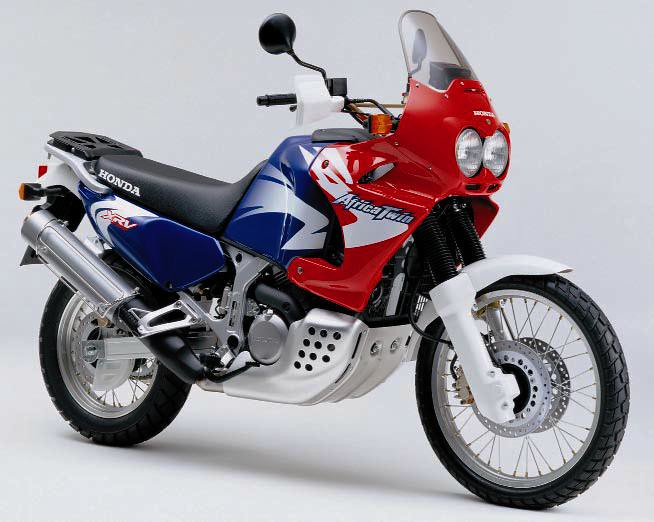
It's never let me down and has enabled me to experience Southern Africa in a way I could never have imagined. The engine still runs with that inimitable V-twin purr, but the creeping at traffic lights, stiff gear-change and oil consumption eventually prompted me to "take a look". Those who have down this road before will immediately recognise the symptoms of motorcyclis restoritis, a debilitating affliction which can only be cured by



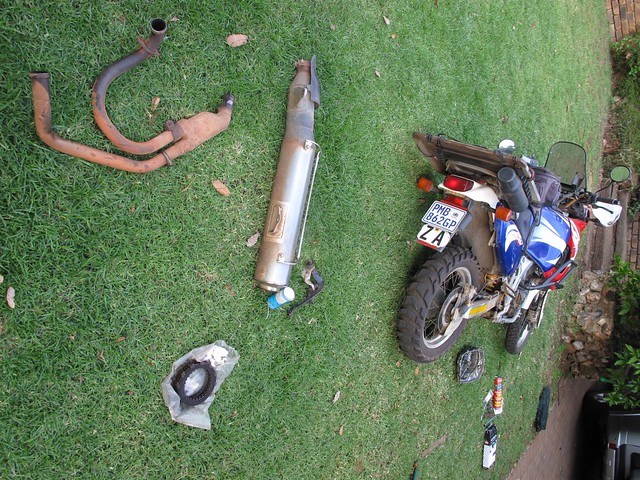
I'm not into bling, and prefer to avoid modifications to my vehicles as they often compromise something else. So the end purpose is simply to get the bike back into a reliable and usable condition for the next hundred thousand km, rather than into a concours or (horror) sellable state.
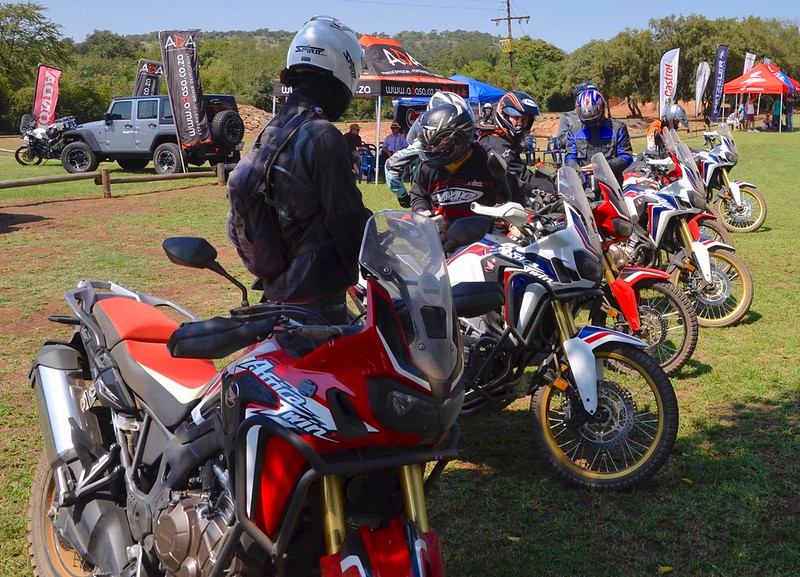
Of course I also did the logical thing and attended the New Africa Twin Road Show and tried the modern reincarnation of my, um, classic version beforehand. It was seductive. I liked the ride, the engine, the ABS... but not the sticker-shock of nearly three times the original price. At moments like these, rational thinking :3some: takes over: my old bike is still fine, It's set up the way I like it, I don't need so much power, all this electronic stuff can’t be fixed in the bush, I'm not riding that much anymore. Etc. etc.
So here is an invitation to join me on my journey of discovery in an attempt to reverse 13 years of accumulated wear and tear.